4 WAYS TO IMPROVE ACCURACY IN YOUR MEDIUM-SIZED DC
Introduction
Maximizing warehouse and distribution center (DC) utilization as well as consistently maintaining peak performance are common goals shared by DC operators. One could imagine it simply starts with identifying and evaluating one’s unique business requirements and addressing the most common challenges with solutions that will deliver the required outcomes. However, with the pace of change in such an environment, it can be challenging for DC operators to consistently deliver positive performance figures against key metrics.
Accuracy: Perhaps the Most Significant DC Challenge
Accuracy is among the most significant issues facing DCs today. It’s no surprise that accuracy occupied two of the top 12 challenges for 2018 per the Warehousing Education and Research Council (WERC) report, including inventory count accuracy and order picking accuracy by location.
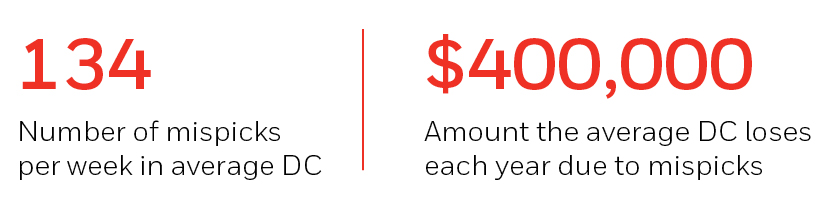
The benefit of accuracy and the cost of inaccuracy are both measurable. For example, DCs report that on average, they experience 134 mispicks per week. This relates to an annual cost of over $400,000 directly related to mistakes, which does not include the potential customer loss.
Industry studies have found the labor cost of a mispick to average $35 and range upwards to $100-plus. This includes repicking labor to go and get the right item, reshipping costs, returns-handling costs, administration for credit cards, and more. These figures become exponentially higher and costlier when one moves into ecommerce.
Ecommerce customers show less loyalty when they experience mispicks and have to return items they did not order. Over 80% of customers would seriously consider switching to a different supplier.
One of the chief culprits for such errors begins with analog or paper-based methods for everyday tasks and workflows. Roughly 25% of North American DCs use this methodology, which is highly prone to errors in every step of the process. Analog and paper-based methods also severely impair receiving, inventory counting, picking, and packing workflows.
DC trends in 2018 show that paper is being taken out of the equation by employing automation and technology solutions – digital transformation. These solutions span radio frequency (RF) scanners, light and voice-directed picking, mobile computers, and
cloud-based services to drive significant efficiency and accuracy improvements.
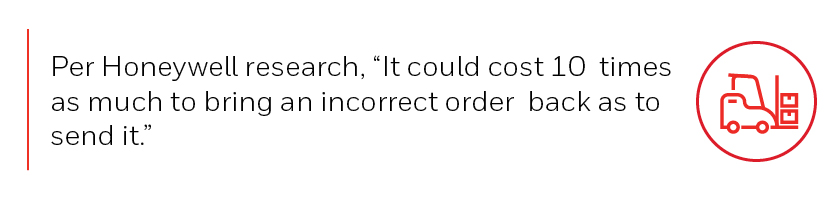